On our "Eco-Tour 23" reportage trip, we stopped off this time at Tatonka, a supplier of outdoor equipment, and let Lukas Treffer, who is responsible for the company's marketing communications, tell us its story and show us around the company's headquarters in Dasing near Augsburg.
From backpack wholesaler to outdoor specialist
In the early days, more precisely since 1980, the business focus of the family-run wholesale company Mountain Sport was on sales for the world's leading backpack manufacturer Jansport from the USA, among others. But soon the plan matured in the company's founder, Winfried Schechinger, to set up a production facility himself. While searching for suitable manufacturing partners, he finally found what he was looking for in Vietnam, so that by 1989 the first of the company's own backpacks were already being sewn. "Own" also because both factories still in existence today in Ho Chi Minh City and in Binh Dinh Province were owned by the Bavarian entrepreneurial family from the very beginning. This enabled the plants to be set up in accordance with European manufacturing standards and the Vietnamese employees to be trained and educated accordingly. High social standards were also established right from the start.
Now the "baby" needed a new name, preferably one that expressed the company's aspirations and characteristics. It should stand for nature, freedom, wilderness and strength, but also express the team spirit. Inspired by the film "Dances with Wolves" and fascinated by the sacred animal of the Plains Indians, the bison, the company was renamed TATONKA in 1993, the Sioux word for this mighty herd animal.
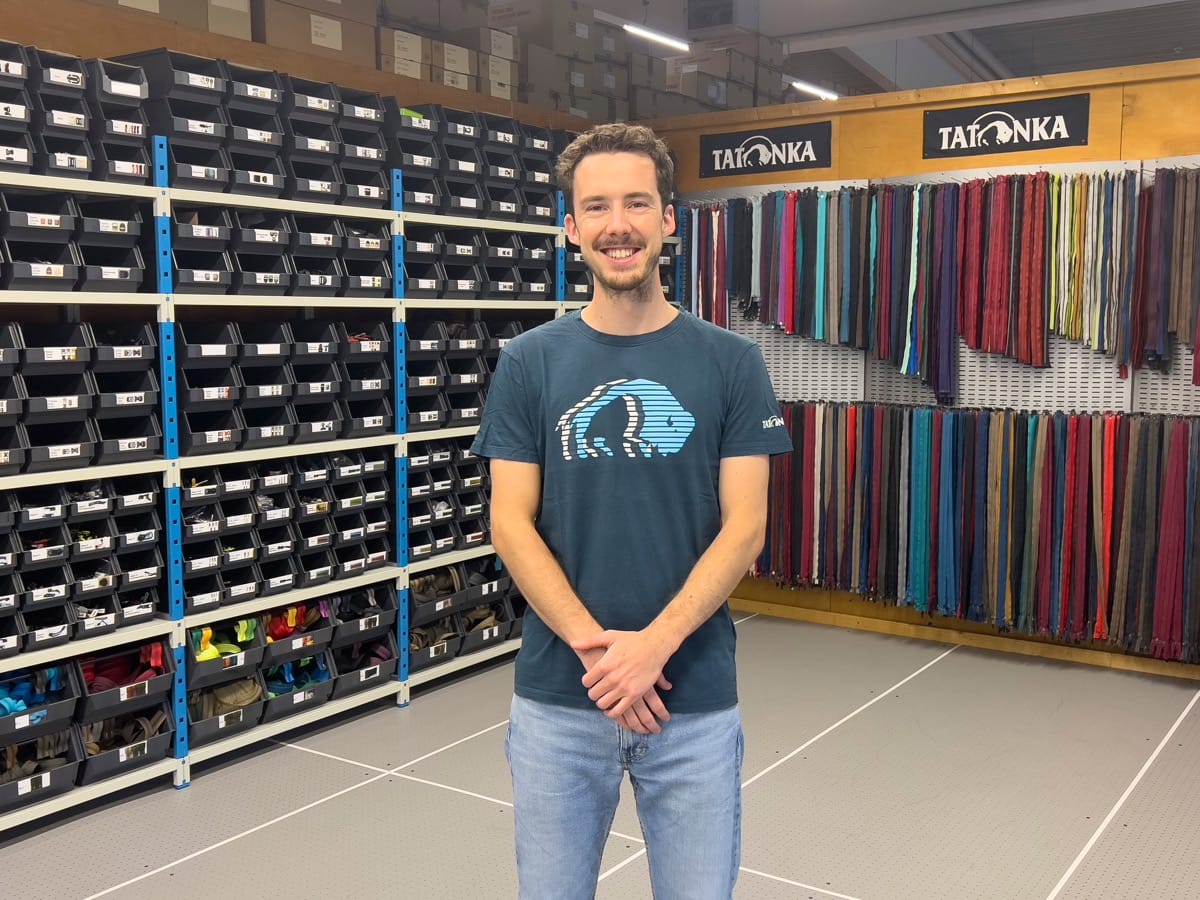
Tatonka now employs 900 people in Vietnam, significantly more than at its German headquarters, where around 70 people are responsible for product development, marketing, administration and deliveries throughout Europe.
In-house production guarantees optimized processes and high social standards
Lukas Treffer reports on the advantages of their manufacturing under their own management. These include "the fact that we can monitor production processes from start to finish, intervene at any time if necessary, respond to necessary changes, and quickly drive new developments forward". Another important aspect is that fair social standards can be implemented and compliance with them monitored far more effectively than would be the case with contract manufacturers with additional subcontractors.
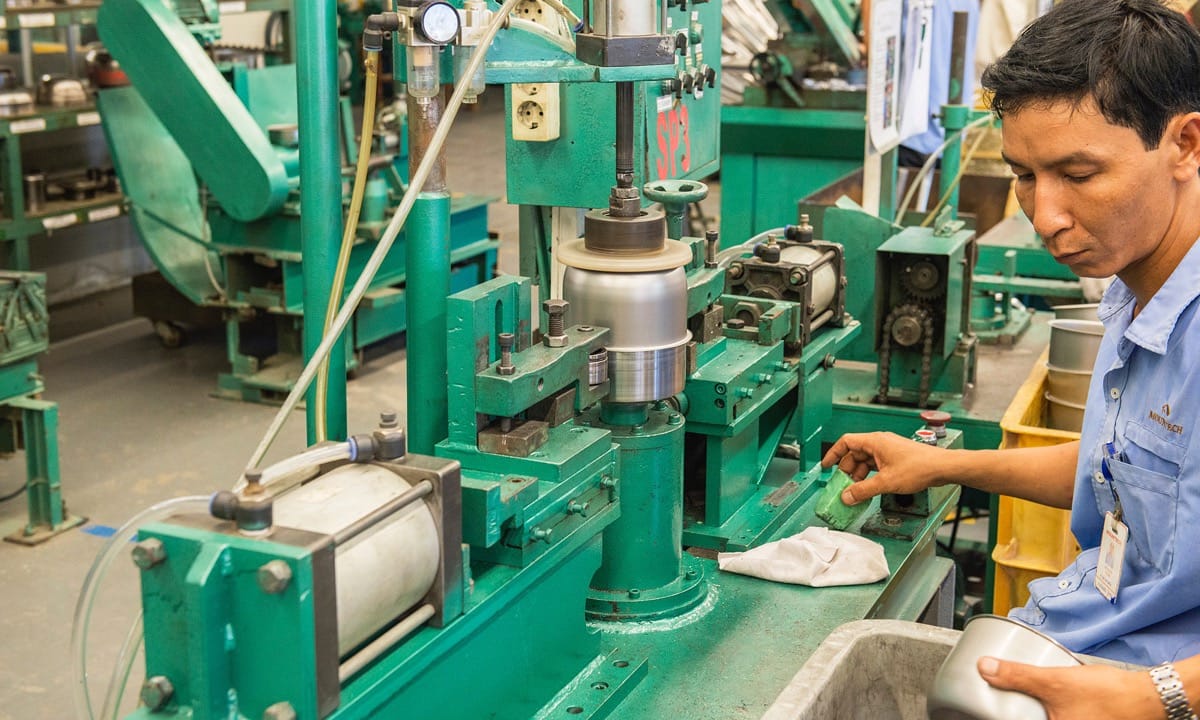
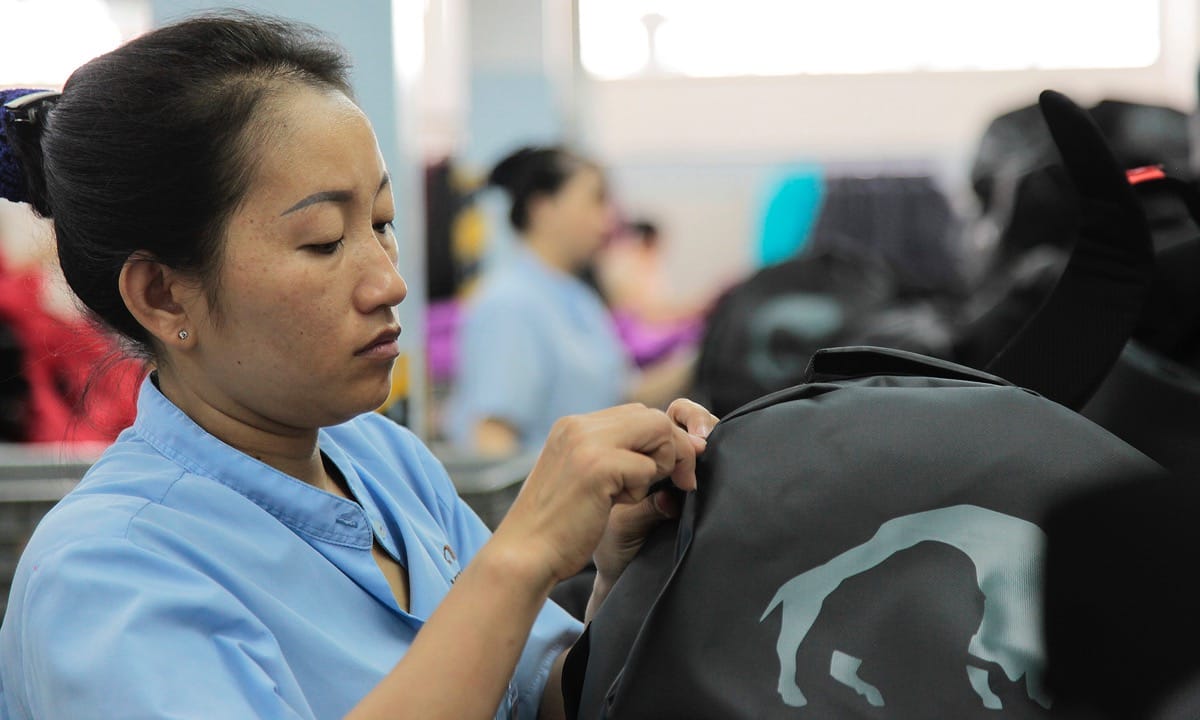
The company's own plant Mountech Co. Ltd. has been certified according to the globally recognized social standard SA8000 since June 2011. In the same year, the European not-for-profit organization "MADE BY" confirmed 100% achievement of the specified social standards. The SA8000 certification is reviewed every six months and renewed after three years, most recently in 2020.
At the "Open Factory" of the plant in the capital, everyone can see for themselves the company's social responsibility towards its employees in Vietnam. Once a week, the factory gates are open to visitors.
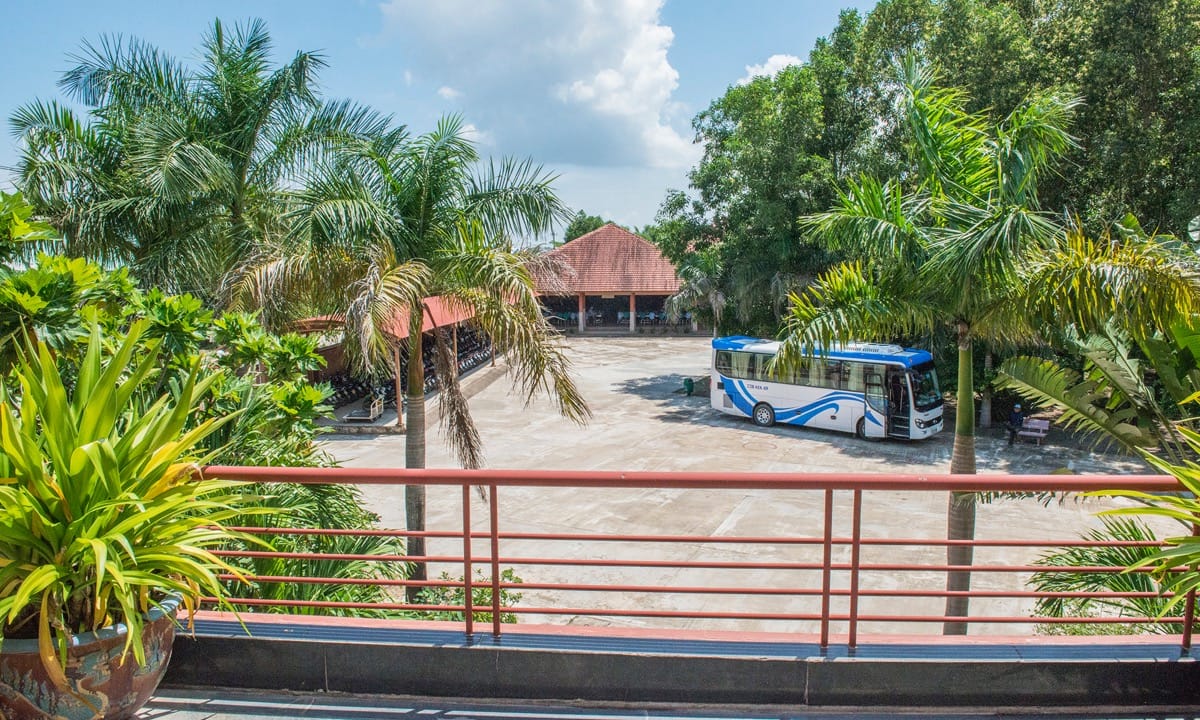
Wide range of products with high quality standards
Tatonka offers a wide range of equipment for "outdoor" activities. As before, backpacks of all kinds form the central product group in the range. Depending on the intended use and users, they are differentiated into those for trekking, climbing, hiking, traveling or for women and children. The portfolio even includes a first aid backpack.
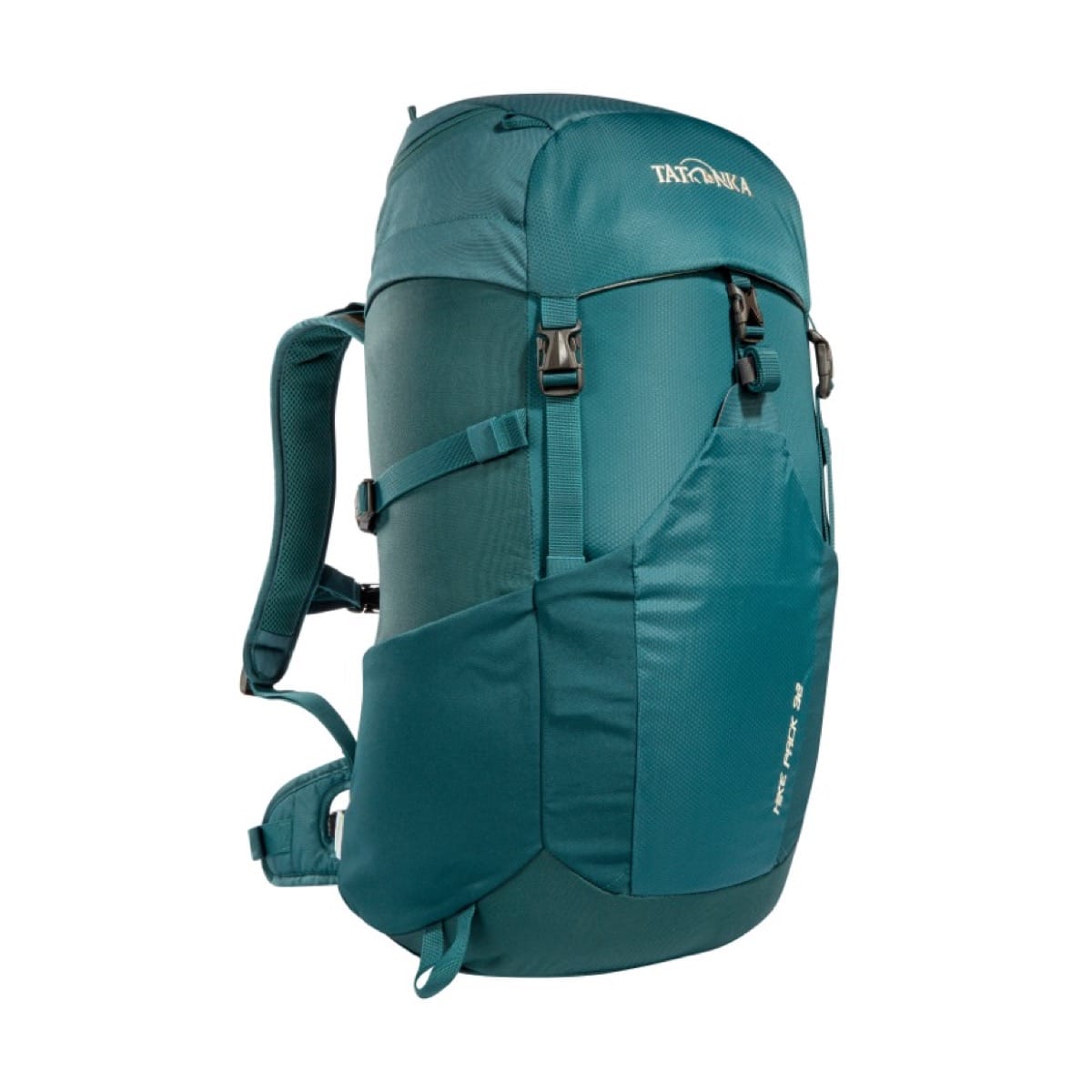
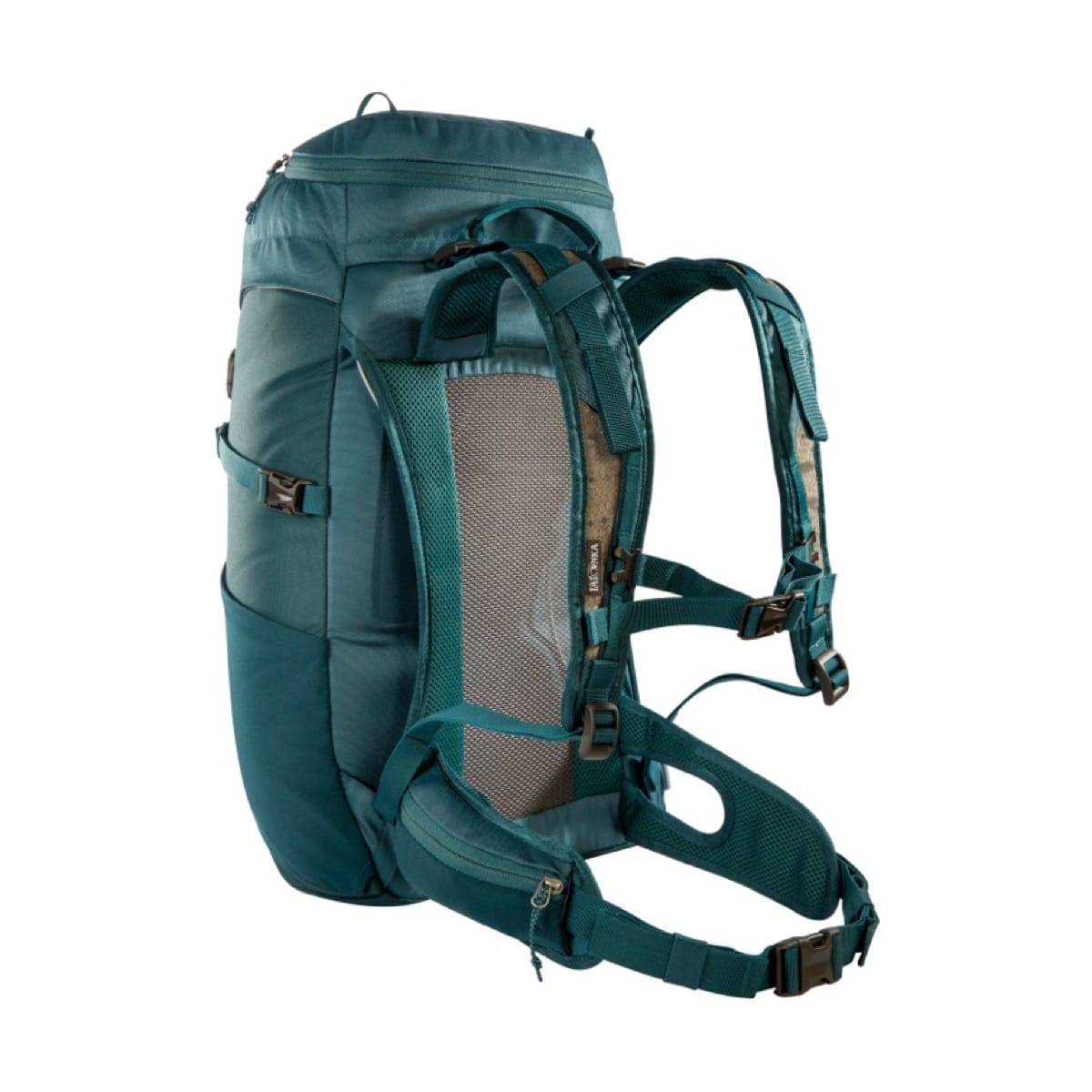
The range also includes travel accessories, equipment for the outdoor kitchen such as plates, bowls, dishes or drinking bottles, outdoor accessories such as rain covers or mosquito repellent and, last but not least, a variety of different tents.
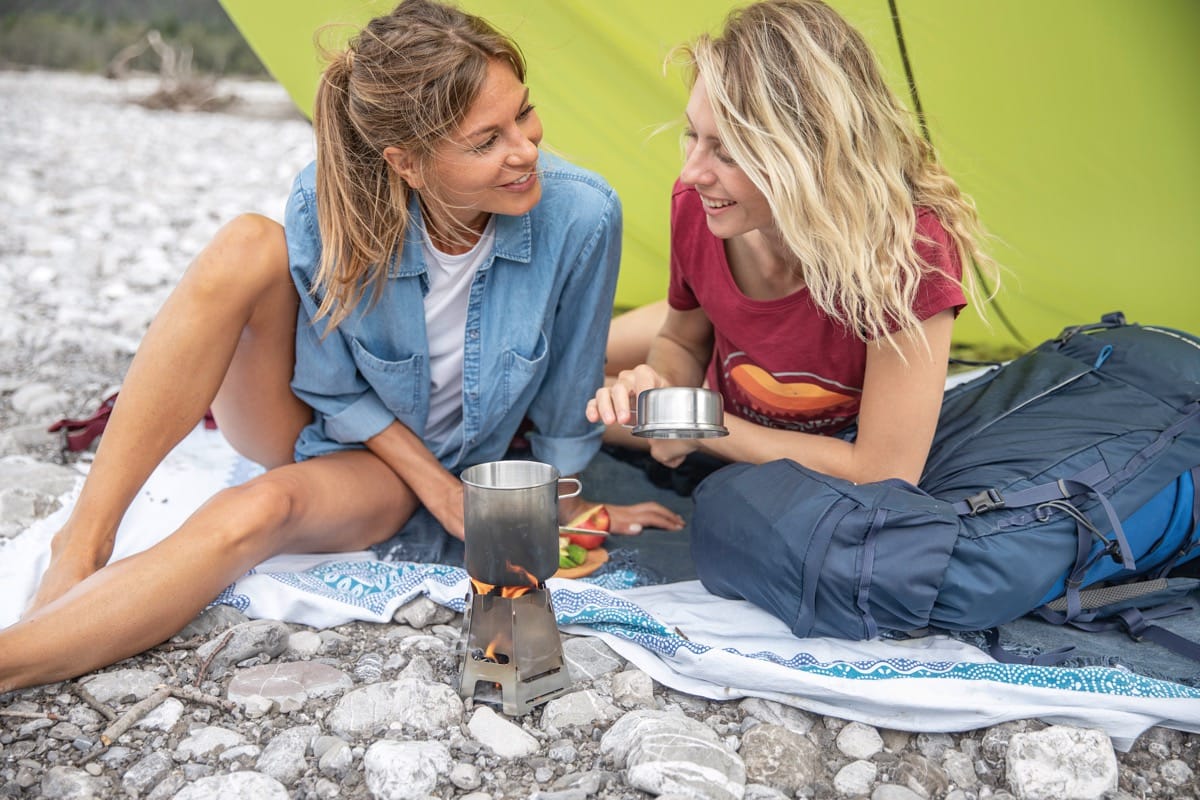
The Bavarian "Bison brand" formulates a high quality standard: "We only use high-quality materials from reputable upstream suppliers with whom we have been working for a long time. This enables us both to ensure consistently high quality and to jointly drive forward material developments. And we insist on the best workmanship."
Longevity as a key sustainability factor
A high quality standard in material selection and manufacturing is the prerequisite for the longevity of articles and this in turn contributes to environmental relief, because what is used and worn over a long period of time does not end up in the trash early and therefore does not need to be replaced quickly. Nevertheless, even with the best products, there is a certain amount of wear and tear or damage to particularly stressed parts over time. However, a broken zipper is by no means a reason to throw away a backpack. That's why a dedicated team at Tatonka's headquarters in Dasingen provides a comprehensive repair service. From the buckle to the tent pole, every spare part is in stock here.
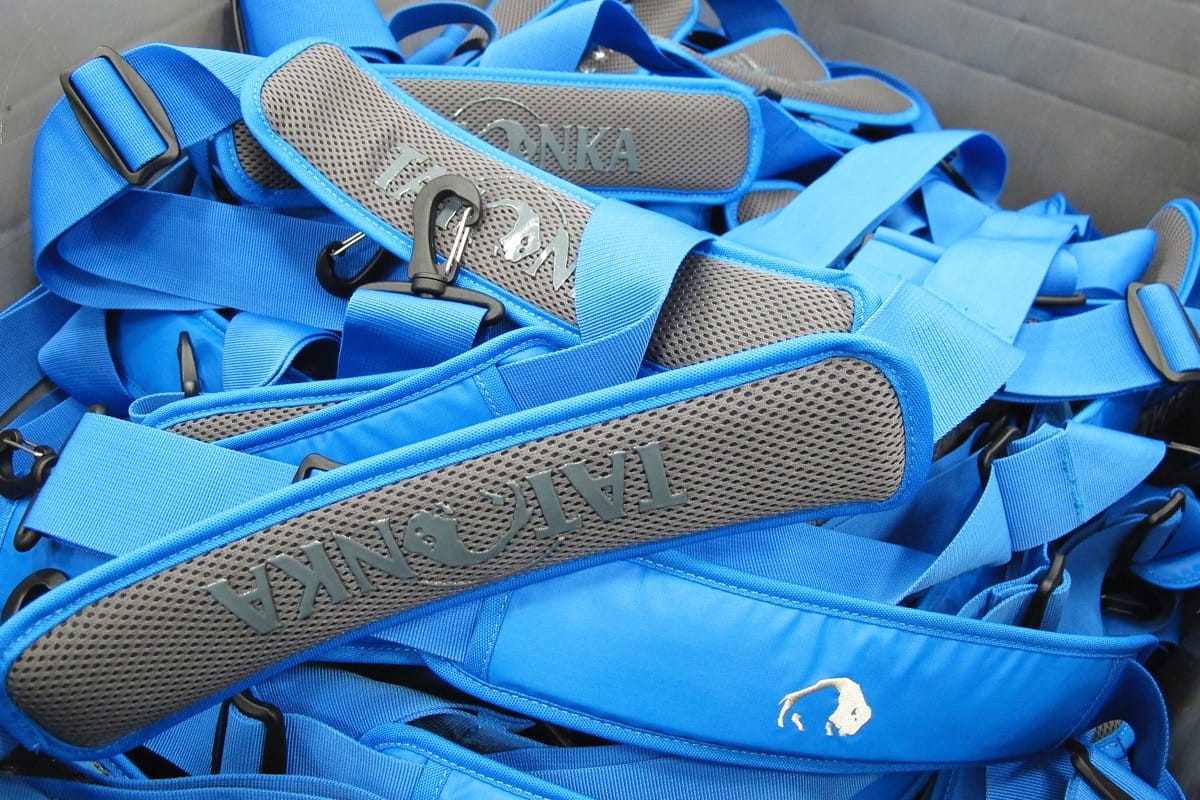
The following repairs can usually be made:
- Replacement of buckles and clasps
- Sewing in zippers
- Replacing pushbuttons
- Replace tent poles
- Mending tent poles channels
- Replacement of webbing, backpack shoulder straps and GRP / aluminum rods.
GREEN BY TATONKA
In order to visibly communicate its own sustainability claim, which is expressed in the slogan "Responsible thinking - sustainable action", Tatonka created the GREEN label. Its purpose is to make it easier for consumers to identify Tatonka products that use sustainable materials. As the manufacturer admits, these materials cannot be used 100% of the time given the current state of technology, but the products are a comparatively more environmentally conscious choice. And they continue to be improved through ongoing developments. The aim is to successively expand the product range with the GREEN label. Already today, the corresponding range includes 187 different articles.
Products with the sustainability label use recycled materials such as recycled polyester or recycled polyamide as well as materials made from renewable, biodegradable and recyclable raw materials such as wool or organic cotton. Likewise the fibers of the Kabok tree, which resemble cotton fibers. Due to their fine structure and your fluffiness, they are also called plant down. From an ecological point of view, the problem-free compostability and the water savings compared to cotton cultivation are particularly positive. Wherever there are sensible alternatives to existing crude oil-based materials, these are replaced by bio-based materials.
Tatonka also makes sure that the suppliers produce the materials used in an energy-saving and resource-conserving manner. These do not contain any substances of concern and are REACH-compliant, i.e. they comply with the European Chemicals Regulation. In the equipment collection, intensive efforts are being made to continuously increase the proportion of PFC-free impregnated products. The PFC-free impregnation of a product is marked accordingly.
Traceability - transparent supply chain
The best recipe for avoiding greenwashing suspicions is maximum transparency. And the Bavarian outdoor outfitter places great emphasis on this. Via the new website Traceability by Tatonka, the path of all products purchased from 2016 onwards can be traced from the purchase of the materials to the production and transport route, as well as the mode of transport.
After entering the serial number, which can be found on the product's label, and the country in which the product was purchased, a world map with a detailed index appears on the website. It is shown from which suppliers the materials used in each case originate and which sustainability certificates the manufacturers can show. The address is also disclosed, as is the start of the business relationship.
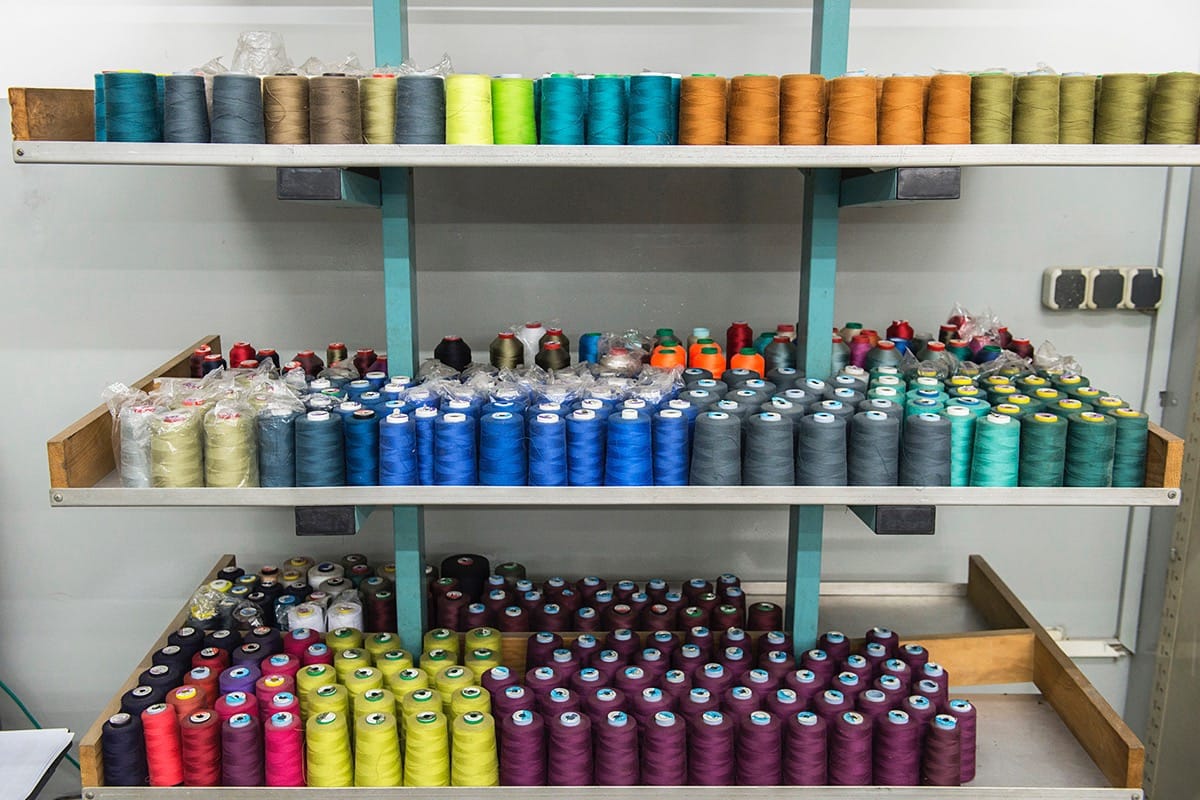
The map then shows the route and means of transport by which the materials are sent to the Tatonka factory in Vietnam. Production takes place at Tatonka's Mountech plant, after which the finished product begins its journey to its destination, traceable in all stages, again showing the transport route and means of transport, for each individual product delivery. It is worth noting that the finished goods are shipped from Vietnam by sea to Hamburg, from there by train to Munich, and trucks are only used for the last leg of the journey to Dasing. Sample collections are shipped by air only once a year to save valuable time.
Due to Tatonka's own production, all steps from the purchase of materials to the transport of finished products are in our own hands and can therefore be controlled efficiently. This opens up the possibility of combining many transport routes. This is done both for deliveries from various material manufacturers to the central warehouse in Vietnam and the loading of two production lines from this central warehouse, as well as for the central export of all manufactured products in one container. This saves resources and reduces CO² emissions.
Self-generated green electricity
Tatonka commissioned a 550 kWp photovoltaic system at its Binh Dinh manufacturing facility in August 2023. The plant with 828 solar panels provides an average of 2300 kilowatt hours of energy per day. The electricity generated is consumed immediately and covers about 65% of the daily needs of the entire production. Due to the uniform solar radiation in the country close to the equator, the plant can be used all year round with almost constant efficiency.
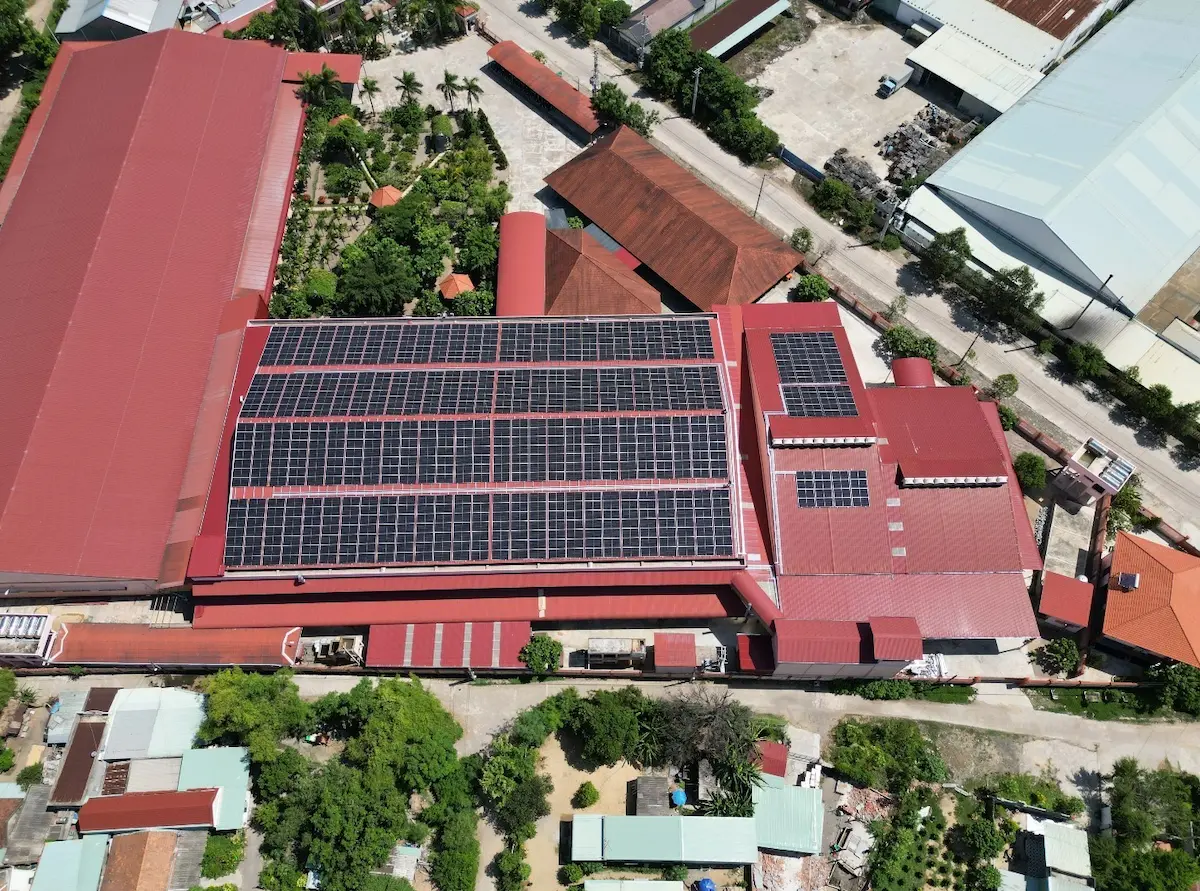
The project was completely self-financed without subsidies, and the plant will pay for itself in a period of about ten years. "It's an investment that pays off ecologically and ultimately also economically - that's how it has to be if you want to operate healthily as a company," says company owner Andreas Schechinger.
A 65 kWp photovoltaic system was installed at the company headquarters in Dasing 16 years ago. 384 solar panels have been feeding CO²-neutral electricity into the German power grid since January 2008 - to date already 1.067 megawatt hours.
Social standards: www.openfactory.tatonka.com
Traceability: https://www.tatonka.com/de/traceability-by-tatonka/
Text: Peter Grett
Images:
Image 1 in text: Peter Grett
All others: Tatonka